10 Ways 3D Printing is Changing Industrial Maintenance
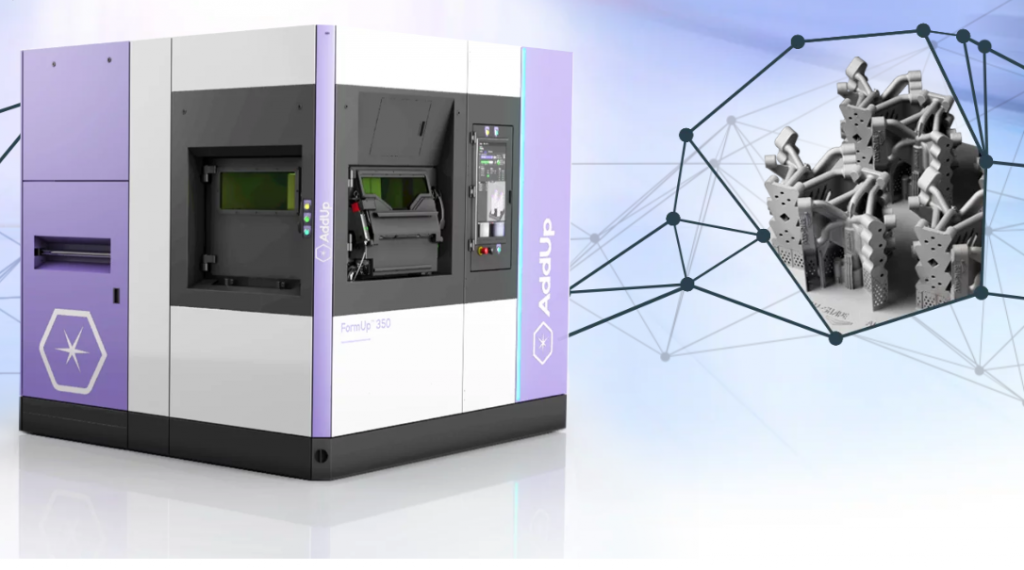
3D printing has transformed the way that industrial parts are made and deployed, creating new possibilities and opportunities in engineering, design, and production. 3D printing reduces the need for inventory by allowing companies to print only what they need when they need it; as well as producing more durable parts that can last longer than their traditionally manufactured counterparts. These are just some of the ways 3D printing has changed industrial maintenance. According to the addup solutions, here we are presenting this list of 10 ways 3D printing will continue to change industrial maintenance in the years to come.
1) Saving Time
Every minute counts in a maintenance worker’s day. With millions of spare parts and tools required to keep various machines, structures, vehicles and buildings operational and running smoothly, time can be a critical factor in getting things back up and running. That’s where 3D printing becomes invaluable; it allows workers to create replacement parts or custom designs that can help save time in maintenance—whether they’re on-site or remotely.
2) Sharing Schematics
Before industrial maintenance workers can fix or install something, they have to know what’s broken. Traditionally, they would have to jot down notes and sketches by hand—or even take pictures with a smartphone—and then use those notes to explain what needs fixing to whoever created their schematics. Now, they can simply send a schematic directly from CAD software to a 3d printing machine like formup.
3) Access to Prototypes
3D printing’s growing popularity means that there are companies that specialize in manufacturing one-off prototypes for inventors and entrepreneurs. When you can’t afford to buy expensive parts and your prototype fails, a quick turnaround time on printed parts can save you valuable time, especially if you have a hard deadline. Many of these manufacturers also offer to work with clients on custom parts—if you come up with an idea for something that doesn’t yet exist, they may be able to help make it real.
4) On-Site Fabrication
The most obvious application of 3D printing in industrial maintenance has to do with its potential for on-site fabrication of spare parts. Rather than ordering a set of custom hardware, you can simply download a digital file and print it on demand. In fact, some companies have even started producing their own components—for example, Airbus has developed a team that produces customized replacement parts for airplanes using one machine.
5) Reduce Costs
If a machine breaks, it’s often expensive to repair, especially if you don’t have any spare parts on hand. With 3D printing, however, technicians can easily produce replacement parts when necessary and quickly have their machinery up and running again. In some cases, they won’t even need to order a new part—they can just print one at home!
6) Diverse Material Capabilities
The 3 in 3D printing stands for three-dimensional, meaning that even though other forms of manufacturing can produce three-dimensional objects, they generally involve manual assembly. Not so with a 3D printer; these machines are capable of producing spare parts and whole components in various materials, some of which may be better suited to certain industrial applications than others.
7) Offsite Printing/Shipping
In a traditional maintenance cycle, an employee would have to leave work and spend several hours (and gas money) going to an offsite manufacturer’s location to get their part replaced. With offsite printing, maintenance employees can simply head over to their printer at lunch or on break and create what they need. This keeps employees on-site, cutting down on labor costs while also creating a more efficient work environment.
8) Personalization
Manufacturers are quickly learning that a one-size-fits-all approach to manufacturing parts for industrial equipment doesn’t work. For many years, large industrial companies would make all of their parts on their own assembly lines or they would outsource manufacturing to a third party. But now it’s increasingly common for industrial companies to turn to 3D printing as a way to create tailored components without producing them in bulk and then storing them away until they need them again.
9) Additive Manufacturing
Applications of additive manufacturing (i.e., 3D printing) in industrial maintenance are growing. A recent report from Wohlers Associates, a company that specializes in additive manufacturing, found that worldwide sales of industrial additive equipment grew 23% in 2014.
10) Perfect Parts Every Time
Perhaps most exciting for engineers, architects, and manufacturers is how additive manufacturing can allow them to create parts with absolutely precise specifications. Why? Because it creates parts by building them up layer by layer (think of a small army of LEGO-style workers). Thus, in theory, all you need to do is design a blueprint of how you want your part to look and then send that information to a printer.